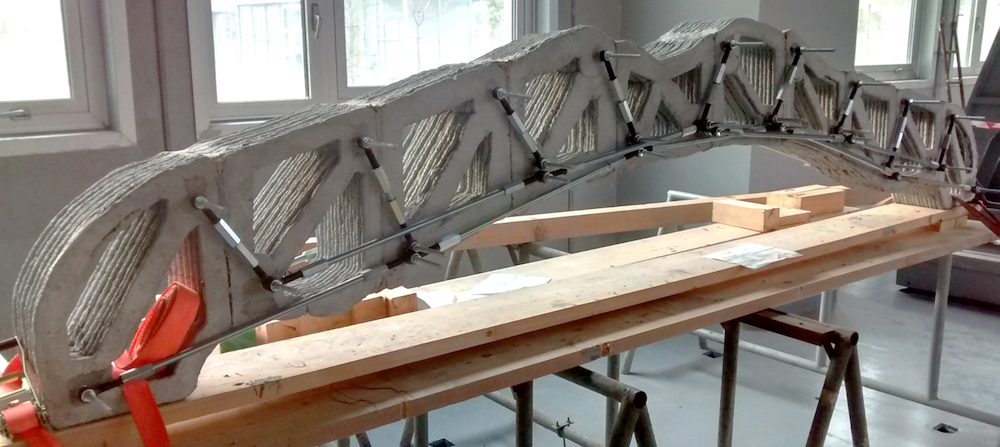
Innovativo, sostenibile, efficiente e flessibile: sono queste le caratteristiche del processo produttivo messo a punto da Etesias, realtà costituitasi nel 2019 a Napoli, per creare nuovi elementi prefabbricati in cemento armato sfruttando le tecnologie di fabbricazione digitale e in particolare la manifattura additiva che utilizza stampanti 3d.
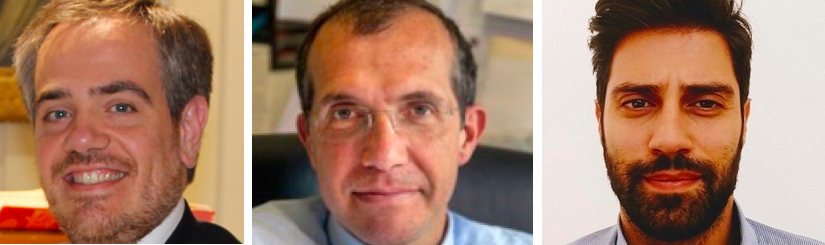
La “mente” della giovane startup è costituita da due professori universitari, Domenico Asprone, professore associato dell’Università di Napoli Federico II, e Ferdinando Auricchio, professore ordinario dell’Università di Pavia, e dal ricercatore dell’Università di Napoli Federico II Costantino Menna. Ed è proprio nel contesto della ricerca universitaria che il tutto ha avuto inizio, per compiere poi un grande passo in avanti grazie all’interesse e al contributo della società Materias, acceleratore di startup, che ha portato l’idea iniziale a concretizzarsi in un prototipo brevettato, la Trave Vesuvio.
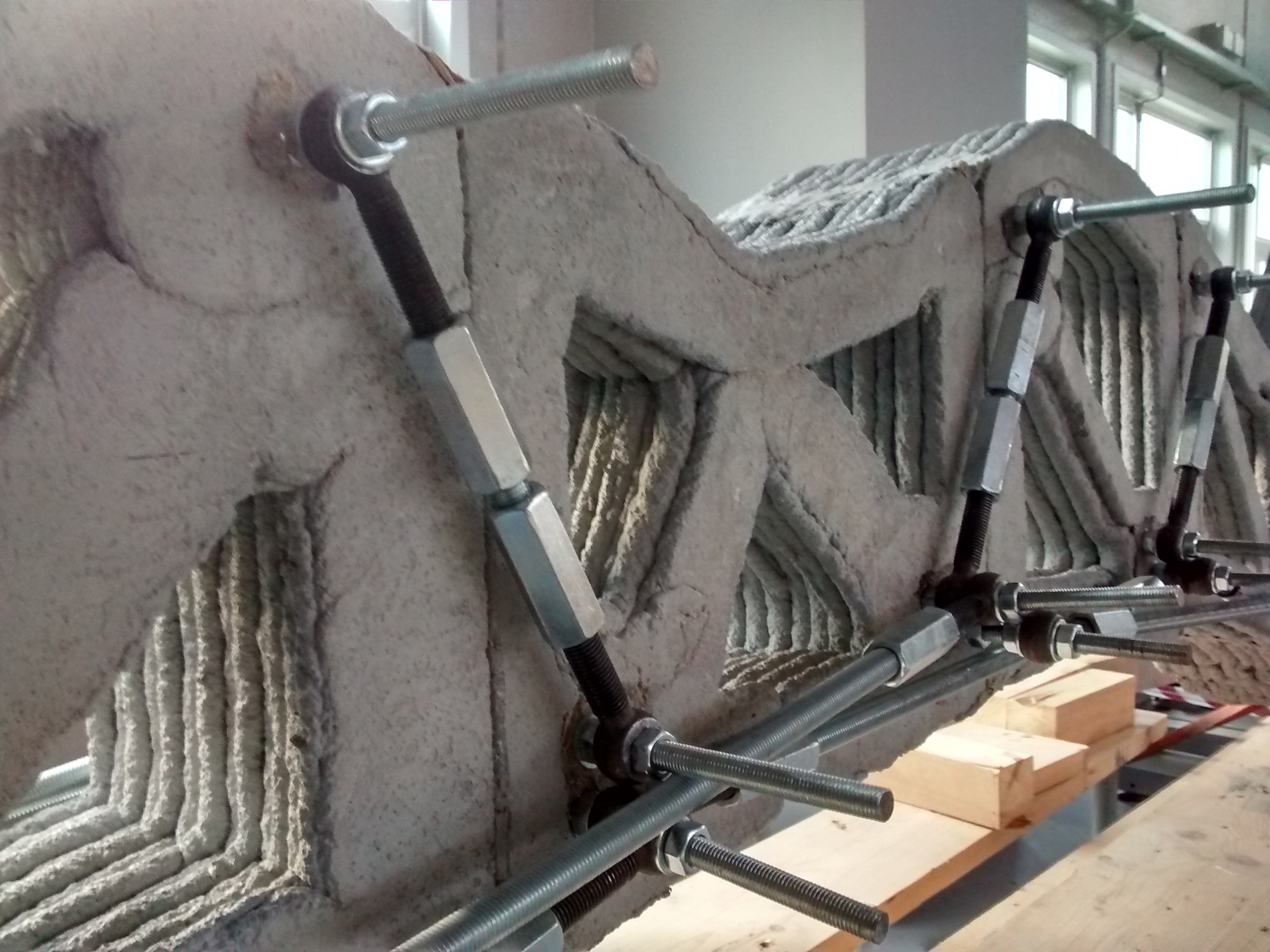
È una trave ad arco in cemento armato, lunga 4 metri, la cui forma articolata ricorda il vulcano napoletano, e caratterizzata da prestazioni meccaniche equivalenti a quelle di una normale trave realizzata seguendo le procedure convenzionali oltre che da un peso inferiore di circa il 50%. Realizzata senza l’utilizzo di casseri, la trave viene assemblata attraverso un sistema che impiega barre in acciaio filettato agganciate all’esterno di conci stampati per un processo di assemblaggio rapido ed efficace.
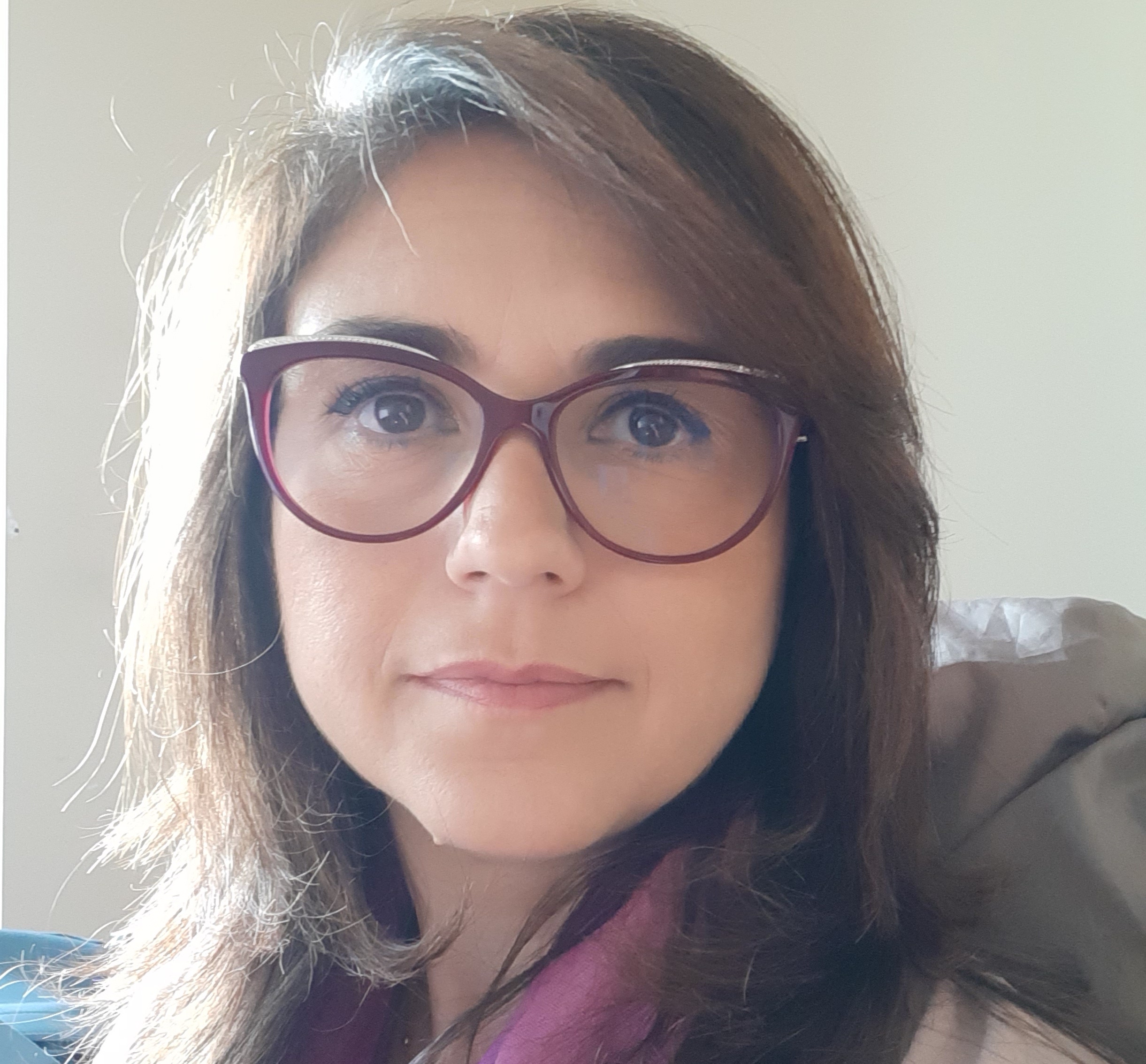
«Il carattere innovativo della nostra tecnologia brevettata risiede nell’impiego della stampa 3d per la realizzazione di elementi costruttivi portanti, con sezione e profilo variabile, caratterizzati da una serie di vuoti che ne ottimizzano le prestazioni meccaniche a un peso nettamente inferiore e quindi a minor impatto ambientale rispetto alle tecnologie convenzionali». Angela Di Ruocco, presidente di Etesias
Tutto questo si traduce in aumento della produttività del 70%, una riduzione dell’inquinamento all’incirca del 50% e una minore produzione di rifiuti (circa il 30% in meno) rispetto ai sistemi di produzione tradizionalmente adottati, grazie al minor impiego di calcestruzzo e all’assenza di casseforme. A questi vantaggi vanno inoltre aggiunti un dimezzamento dell’impiego di materie prime e una diminuzione del 30% dell’energia utilizzata, a parità di prestazione meccanica rispetto ai sistemi attualmente in uso, oltre alla possibilità di realizzare elementi strutturali prefabbricati smart e personalizzabili. Sfruttando le potenzialità della tecnologia firmata Etesias e della stampa in 3d sarà possibile costruire infrastrutture sempre più sostenibili aprendo così nuove possibilità al futuro delle costruzioni.

«Il processo realizzativo – aggiunge Di Ruocco – è unico nel suo genere; sebbene esistano altre tecnologie per la realizzazione di elementi in calcestruzzo con stampa 3d, sono pochissime le applicazioni sviluppate per la realizzazione di elementi in cemento armato con funzionalità strutturali e peraltro con tecnologie più complesse e meno versatili». Etesias punta così a offrire al mercato alternative semplici, innovative ed efficienti, mantenendo però le stesse performance garantite dai metodi tradizionali dell’industria del calcestruzzo «ma un costo nettamente inferiore alla media del mercato, sfruttando una tecnologia all’avanguardia in tanti altri settori industriali che possa portare a un aumento della produttività, una contrazione dei costi fissi e un impatto ambientale ridotto», precisa la presidente di Etesias.
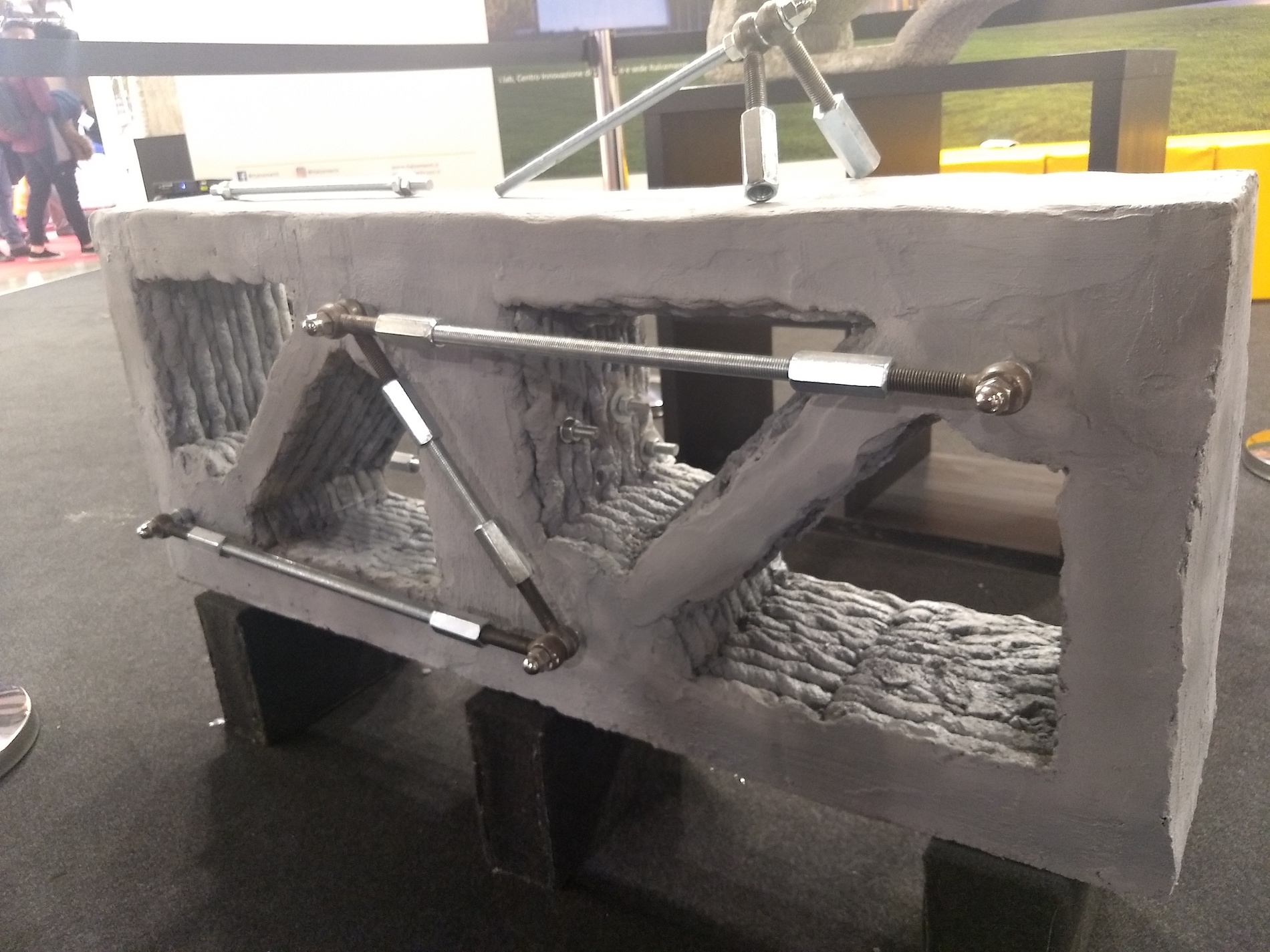
Un progetto che guarda al futuro e che ha suscitato l’interesse di Italcementi, tra i principali produttori di cemento e calcestruzzo, con cui la startup di Napoli ha stretto un accordo di collaborazione sul fronte ricerca e sviluppo con l’obiettivo di implementare ulteriormente la tecnologia messa a punto da Etesias nei laboratori di San Giovanni a Teduccio (Na).
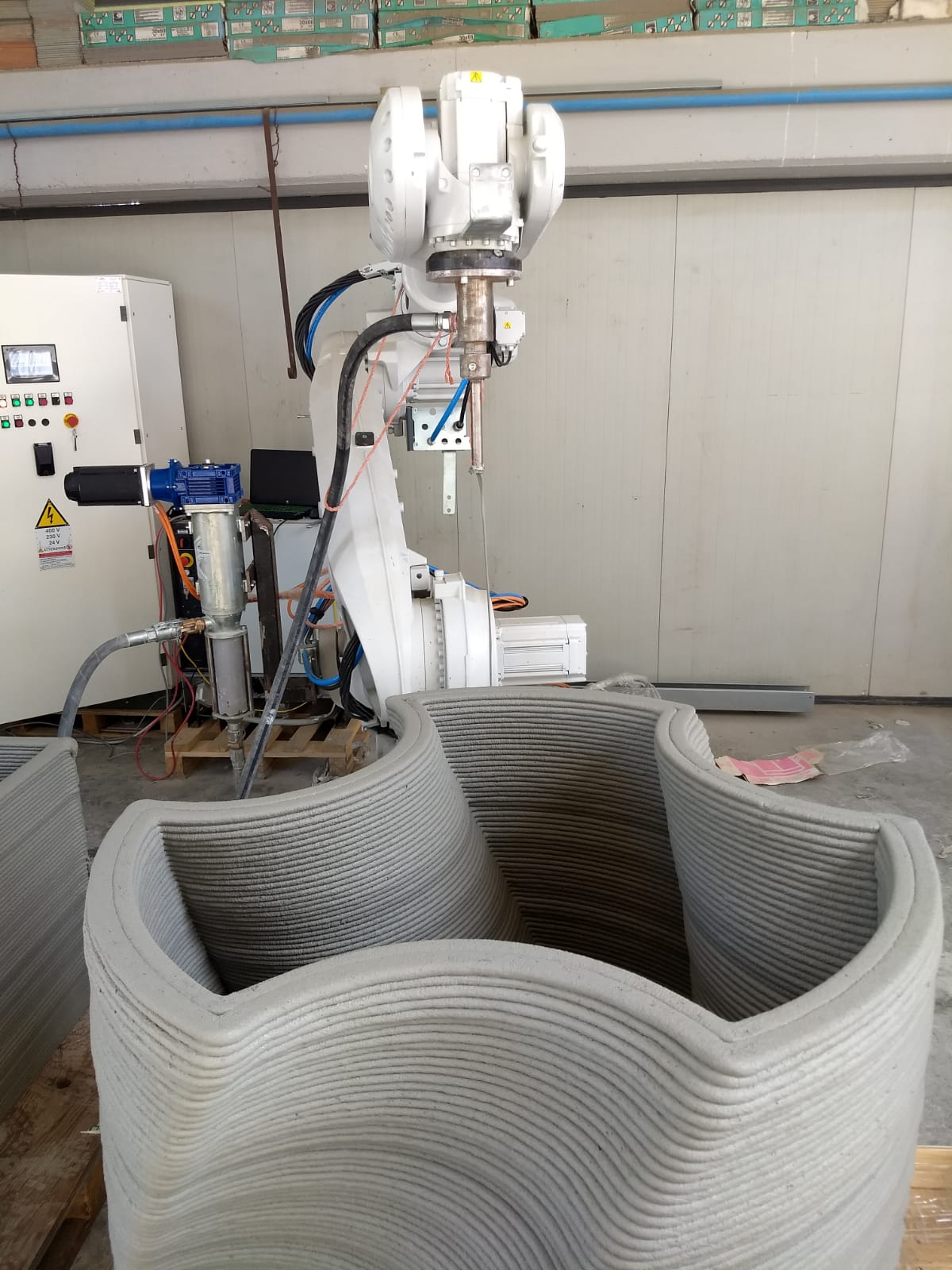
Un primo e rilevante contributo di Italcementi è consistito nell’acquisto di un impianto pilota di stampa 3d con braccio robotico e con un sistema di miscelazione e pompa per calcestruzzo, installati a Napoli. Grazie a questo impianto, Etesias e Italcementi «continueranno ad accrescere il comune know-how tecnico per perfezionare tutti gli aspetti di un processo produttivo che allo stato attuale risulta già essere innovativo, sicuro, efficiente, veloce e flessibile», conclude Angela Di Ruocco.